Economiser Coil
Flue gases, a byproduct of boiler combustion, take away heat that is frequently left unused. To harness this untapped energy, economiser coils are positioned strategically along the flue gas route. As hot flue gases flow through the coils, they transfer their thermal energy to the fluid, usually water. This captured heat is then recycled back into the system, preheating the feedwater before it enters the boiler.
Bending Techniques
Cold Bending with Booster Techniques
This procedure achieves a bend radius that matches the tube diameter (R/D ratio of one). This ideal curvature lowers pressure drops, promotes efficient fluid flow, and improves heat transmission. To prevent tube collapse or deformation, we use unique "booster" procedures during cold bending.
Hot Bending for Tighter Spaces
We use the hot bending technique when there is limited space within the boiler. This strategy allows us to attain tighter bend radii while staying below an R/D ratio of 1. Our economiser coils integrate perfectly into any boiler arrangement due to their bendability

Product Benefits
While the core functionality of economiser in boiler focuses on waste heat recovery, they offer additional benefits:

Reduced Emissions
While the core functionality of economiser in boiler focuses on waste heat recovery, they offer additional benefits:

Improved Boiler Efficiency
Preheating the feedwater reduces the energy required in the furnace to achieve the optimum steam temperature, resulting in significant cost savings and a more sustainable boiler operation

Extended Boiler Life
With a tolerance of +3 millimetres, our bend panels are precisely produced to an exceptional degree of straightness. This degree of precision ensures that water or steam flows through the tubes as efficiently as possible, reducing pressure drops and increasing boiler efficiency.
At RIBO, we offer a variety of designs and combinations to meet the individual requirements of each boiler system. Factors such as tube number and arrangement, finned tubes to increase heat transfer surface area, and material selection based on pressure, temperature, and flue gas composition are all considered to provide the optimal solution.
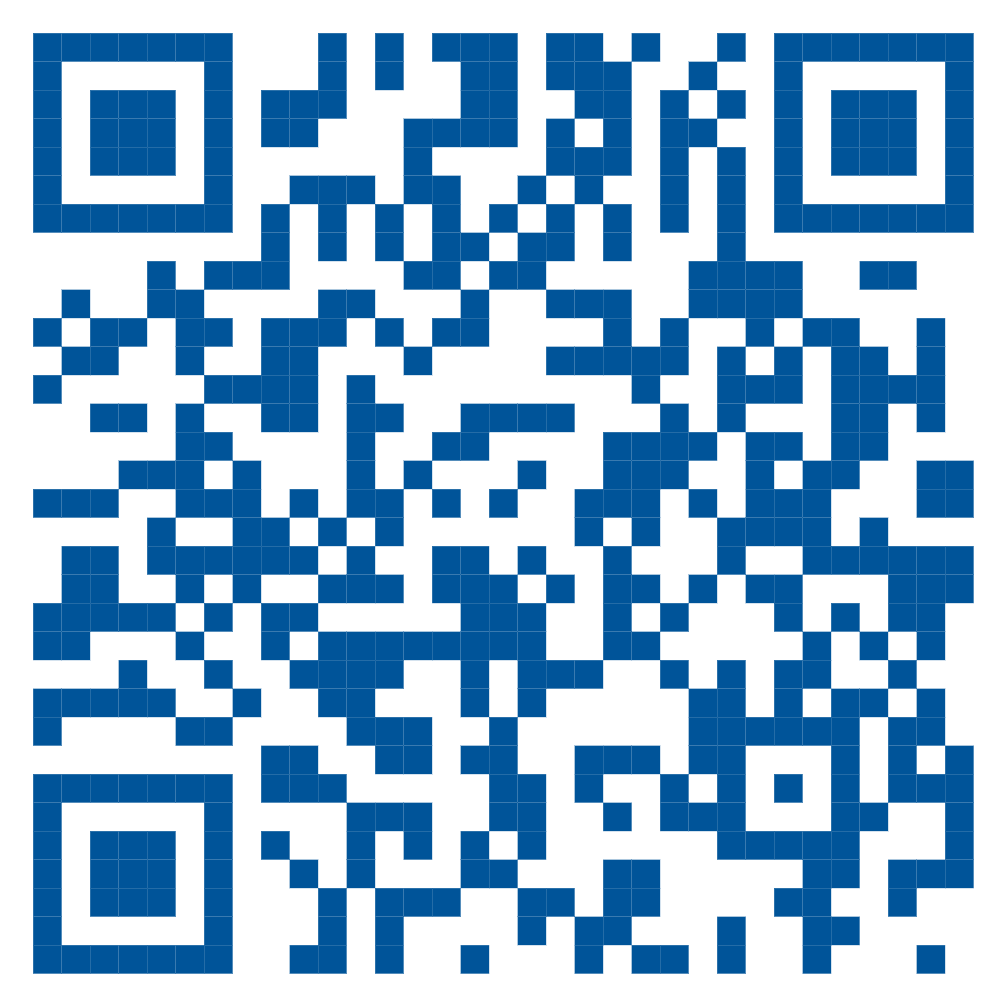
If you are looking for more information or clarification, just fill in the form and our team representative will get in touch. You can also chat with us on whatsapp, by simply scanning the QR code below or call +91 94421 42112
Your Information is secure with us.
we do not share or sell contact information
Corporate Office
RIBO Industries Private Limited
#9, 1st Main Road, Raja Colony, Cantonment, Tiruchi 620001, Tamilnadu, INDIA.
+91 944 214 2112 | marketing@ribo.in | +91431 – 2402112
Quick Links
ASME (S) (U) | ISO 9001 | ISO 14001 | ISO 45001